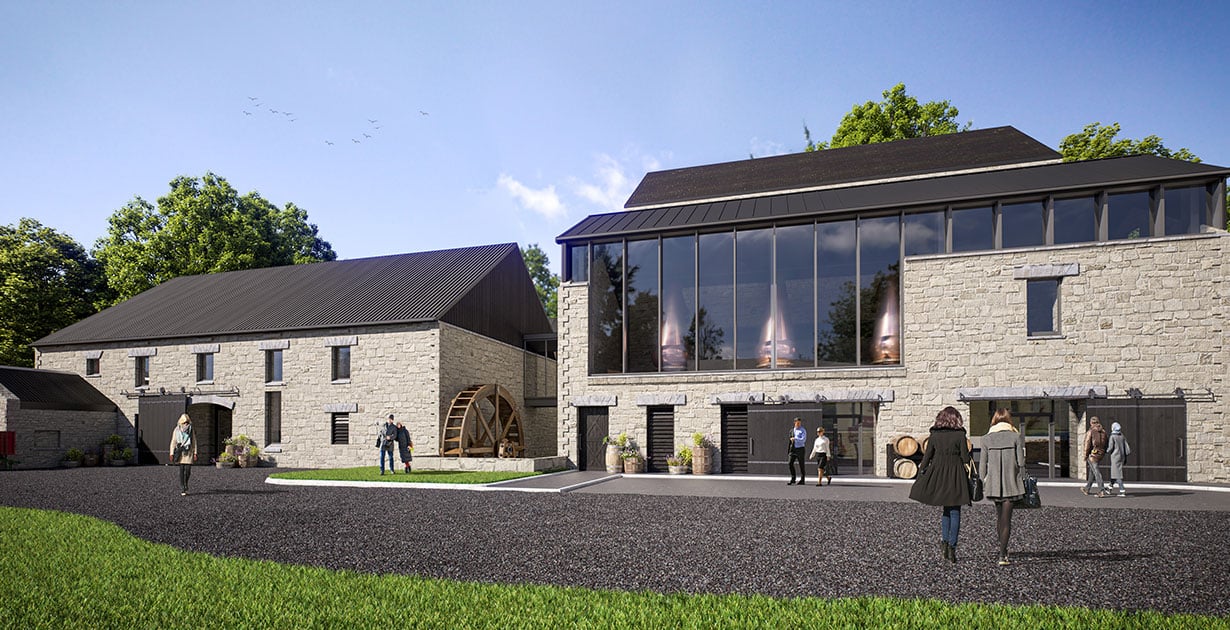
In a world where tradition reigns supreme, Ahascragh Distillery in County Galway is shaking up the whiskey industry with its innovative approach to sustainability. As Ireland’s first eco-distillery, Ahascragh combines cutting-edge technology with a strong community focus, proving that modern techniques can coexist with time-honored craft.
Founded by Gareth McAllister, Ahascragh Distillery is redefining whiskey production by using a low-energy, zero-emission process powered entirely by renewable energy. Beyond its technical innovation, Ahascragh is revitalizing its rural community by creating jobs and offering locals a financial stake in the distillery. This article explores how Ahascragh Distillery is transforming not only how whiskey is made, but also how distilleries can positively impact their environment and community while maintaining the craft’s integrity.
New Whiskey
Things used to be so simple. We were told that whiskey was good when it was old… the older, the better. In the past five years, this has been shown to be a myth – young whiskeys can have heft, interesting character, and good flavor. Bars are now lined with bottles from a new generation of high-quality whiskeys that can hold their own alongside the legacy names.
These new whiskeys come from spirits that are produced to age quickly, with the casks and their careful management adding character.
Increasingly, it is becoming more important for distillers to produce whiskey in a sustainable way. By changing the whiskey maturation schedule, distillers can produce high-quality goods and reduce the environmental impacts of long-term maturation such as energy consumption in maintaining warehouse conditions.
The Push For Sustainable Spirits
Despite all the recent investment in new distilleries, most of these new whiskeys are produced in exactly the same way as they have been for decades. Malted barley is washed with hot water in a mash tun, the liquid mash is cooled for fermentation so it doesn’t kill the yeast before it can make the wash, and then the wash is boiled to release alcohol vapors, and then cooled again during condensing.
It’s a very energy-intensive process of heating and cooling, which was established in a time of much cheaper energy. Efficient production means that a lot of heat must be lost in a hurry, so every distiller ejects heat into the atmosphere using cooling towers and electrical chillers. It doesn’t take an expert to understand that this is a terrible waste of energy.
Many in the industry are now adding complex heat recovery and energy efficiency technology to their existing equipment, but the fundamentals are unchanged. They can only squeeze a certain amount of efficiency out of the old ways of doing things, which can only save so much energy.
Ahascragh Distillery – Doing Things Differently
The stillhouse. Credit: Ahascragh Distillery
Sometimes it takes someone from outside an industry to try something new, especially one with legend and legacy at its heart. Step forward Gareth McAllister, the owner and developer of the new Ahascragh Distillery in County Galway, who brings with him a background in the pharmaceutical industry. Distillation and the production of pharmaceuticals share many similarities, providing Gareth with a firm understanding of the technical side of the new distillery project. He didn’t need to heed industry lore.
Ahascragh Distillery calls itself Ireland’s first eco-distillery. It is sustainable in many respects; the benefits to the local community, the way that the spirit is made, and even the way that the distillery was funded.
Community Benefits
Like many distilleries, Ahascragh has become the largest business in a small rural community. Having good standing with the neighbors is, therefore, essential as local businesses have done for generations.
This relationship takes on many forms, from employment to ownership. Local people suddenly have access to good jobs close to home. The business opened a café and bottling hall over the road from the distillery before it was even complete. There are now 15 people directly employed, with up to 60 jobs supported in the wider economy, a significant number for a rural village of 200 people.
The distillery has converted a traditional mill building, even replacing the former water wheel, taking the design from salvaged parts found during construction. For years the mill had lay ruined in the heart of Ahascragh village. It struggled to find an owner, with few potential users able to make use of its large industrial spaces, and being a protected historical structure, it couldn’t be radically altered. As many new whiskey makers have found out, a large mill building is ideal for them, easily housing its large vessels, silos, tanks, and pot stills.
In refurbishing the mill, the business gave new life to the building around which the village had formed. It didn’t stop there, however. The business gave locals the opportunity to invest and take a stake in the financial future of the business through a crowdfunding process, which raised a significant part of the overall investment.
Low Energy Distilling At Ahascragh Distillery
An impression of the make up of the distillery. Credit: Ahascragh Distillery
Ahascragh has developed a new way of making spirits, giving zero emissions. It proudly says, “There is no chimney”, unlike every other distillery. It is all-electric, with the power coming from renewable sources, either from solar panels on its roof or purchased from other sustainable sources.
In making this spirit no heat is ejected to the atmosphere; all heat is reused. It is reclaimed from the waters used to cool the fermenters and the condensers, then increased in temperature using a high-temperature heat pump. This higher-temperature water is then used to boil the alcohol in the stills. Heat is taken out of the condenser cooling water, and the cycle starts again. Whilst domestic heat pumps generally have a coefficient of performance of 3 or 4, meaning 3 or 4 kWh of heat is generated for every 1 kWh of energy input, this system has a CoP of 6.5. It is ground-breakingly efficient.
Until very recently this couldn’t have been done, no heat pump could reach the temperatures required for distilling. The technology is brand new. The Finnish supplier Oilon supplied this new, very high-temperature heat pump, which allows Ahascragh to use only one-third of the energy of a traditional distillery overall.
Does It Work?
The industry has been watching closely to see the results of this multi-million-euro experiment. The distillery says that every distiller in Ireland has been through their doors.
Like others in the industry who are investing in groundbreaking systems, they are entirely open about what they are doing and how it is performing. They are sharing their results to allow other producers to learn and develop the technology further.
Of course, the additional investment in the heat pump technology must reduce fuel costs sufficiently to make it worth the investment. At this stage, over a year into distilling, the signs are very good.
Here is a business that has redefined the traditional way of Irish whiskey making, whilst regenerating a village, creating jobs, and giving locals the opportunity to have a financial stake in their local business. Luckily the new spirit is every bit as good as doing it the old way.